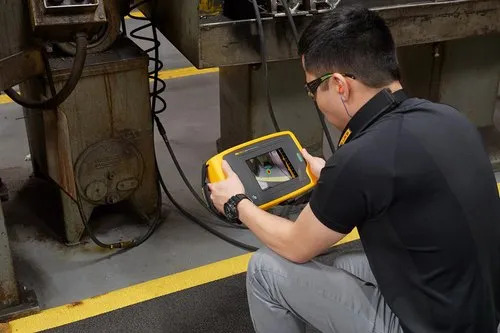
Compressed air : It is one of the most expensive utilities and the cost to operate also very high.
- This is one of the largest uncontrolled Utilities at many facilities.
- Looking at the high rise in electricity cost and power crises looming, in order to keep a tight leash on the operating cost, it is imperative that the facility conducts an Air Audit of the system internally on a regular basis and through an external agency as and when required.
- The audit would mainly focus on optimization & energy conservation from the compressed air system.
- It will help in finding out the following in the compressed air system
- Actual demand and the efficiency, at which the present system is operating,
- Power consumption, individually and for overall system
- Average supply pressure.
- Minimum pressure required.
- Leakages in the system, you can track, asses, quantify and document losses
- It is very important to measure without which improvement becomes very difficult.
Measurements and Data Collection
There is a range of measurement methods available to auditors.,which is required to select the appropriate measurement technology, depending on the particular compressed air installation and the technologies being used.
- Electricity Usage Measurements : three-phase electricity meter (with data-logging capability) should be used to directly record kilowatt (kW) and kilowatt hour (kWh) usage.
- Pressure Measurements: Pressure should be measured at the compressor: at points where the main users of compressed air exist; , and other locations where pressure drops are likely to be observed .
- Flow Measurements Knowledge of the air flow is important to understand a compressed air system’s delivery performance.
- Intrusive flow meters
- Non-intrusive ultrasonic flow meters
- Air Leak Detection: For an ‘investment level’ audit of a compressed air system, it is expected that ultrasonic leak detection (performed by an appropriately skilled operator) is performed to quantify air leakage. Operators of the ultrasonic equipment,

On-site Measurements and Data Collection
- Site-level Data Collection
- Under stand Actual Compressed air Requirement of the System
- Compressor Operating Characteristics analysis
- Actual Demand Measurements Analysis
- Supply Measurements Analysis
- Network Measurements :pipework configuration and sizing analysis
Data Analysis
- Demand versus Requirements
- Dryers, Condensate Drains and Oil-Water Separators
- Compressed Air System Network
- Air Balance and Energy Balance
COMPRESSOR AUDIT OUT COMES :
- Operating costs of compressed air systems (which, the world-wide experience shows, can be reduced by 5 - 50% of their current levels or more)
- Productivity (which, can be greatly improved by eliminating such problems caused by compressed air such as poor product quality or reduced plant output due to low air pressure, poor air quality or unreliable operation)
- Future capital spending can be cut back by getting the existing system to run more effectively (the truth is that most systems have too much capacity and it’s the lack of information and the lack of an appropriate strategy that forces customers to buy more compressors when problems arise)
We have extensively trained auditors specifically for carrying out detailed study of the compressed air system, who in their own capacities have 8-15 years of hands-on experience in the field of compressors. They are equipped with the latest tools and instruments such as energy & flow meters, pressure & current loggers (capable of recording more than thousands of data-points that can be trended and analysed by our experts) etc.
Compressed Air Flow Meter Installation Procedure
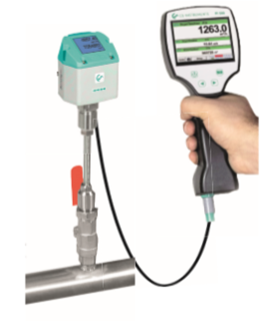
Equipment Details :
- Purpose / Objective : To measure Flow (m3 /sec or CFM) for compressed air and gases
- Result: Efficiency/FAD Analysis of compressors
- Model : - PI 500 - Portable Flow Meter & VA 500 - Flow meter
- Make: CS instruments, Germany
- Accuracy: ± 1.5% of measured value. ± 0.3 % of full scale
- Flow measurement
- Pressure-/ vacuum measurement
- Temperature measurement
The portable flow meter PI 500 is an all-purpose hand-held measuring instrument for Compressed Air and gas applications in industry like
Compressed Air MEASURED Flow IN CFM
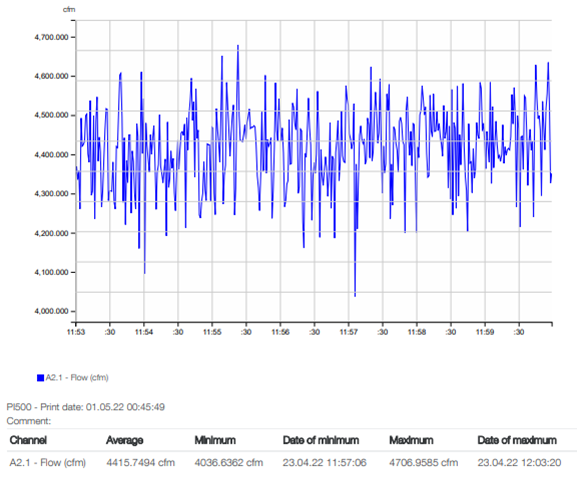
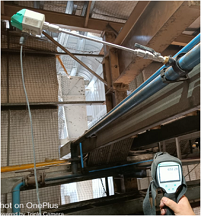
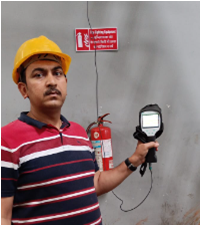
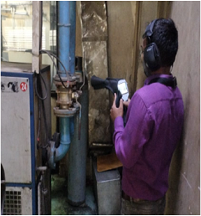
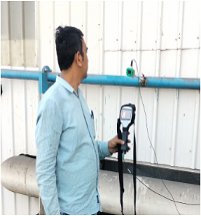
Compressed Air Flow Meter Principle of Operation:
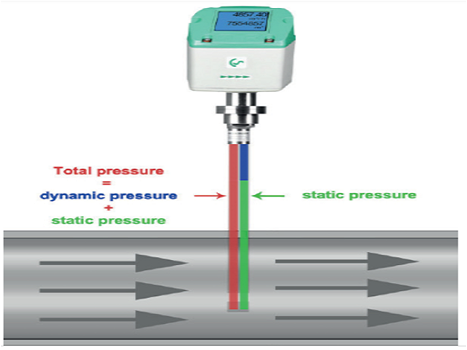
Principle of Operation:
- The integrated, precise differential pressure sensor measures the differential pressure / dynamic pressure at the sensor tip.
- The pressure depend on the respective gas velocity.
- The flow is therefore easy to determine by means of the pipe diameter.
- Make: CS instruments, Germany
- The additional measurement of temperature and absolute pressure and calculation of the relevant density means that measuring can be carried out for various gases, a wide variety of temperatures and pressures.
Installation of measuring point:
Inlet / outlet runs
- In order to maintain the accuracy stipulated in the data sheets, the sensor must be inserted in the centre of a straight pip e section with an undisturbed flow progression.
- An undisturbed flow progression is achieved if the sections in front of the sensor (inlet) and behind the sensor (outlet) are sufficiently long, straight and without any obstructions such as edges, seams, curves etc.
- Therefore, it is necessary to ensure the recommended inlet and outlet runs.
- Make: CS instruments, Germany
- The values represent the min. lengths. In case the min. inlet / outlet runs could not be ensured, it must be expected to get increased or significant deviations of the measurement values.
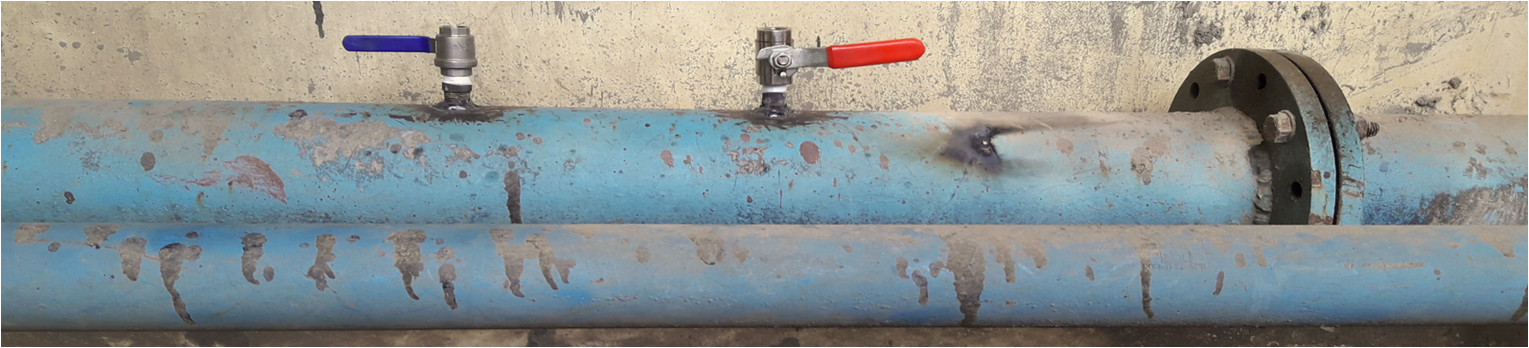
Simple installation and removal under pressure:
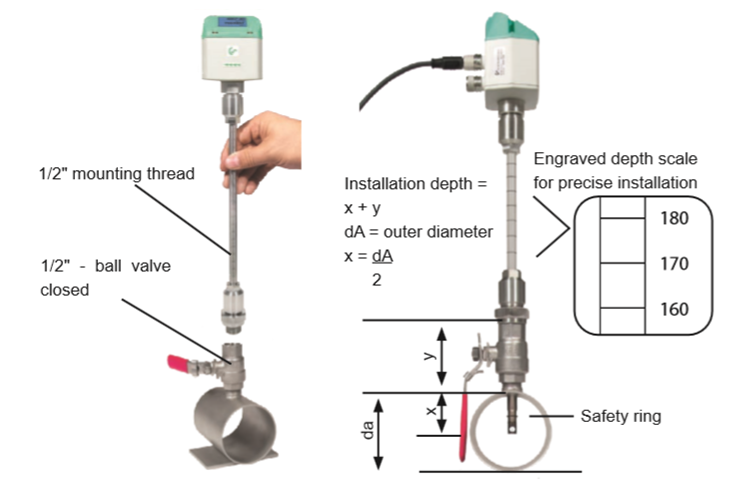
- Even under pressure, the flow probe VA 500 is mounted by means of a standard 1/2" ball valve.
- During mounting and dismounting the safety ring avoids an uncontrolled ejection of the probe which may be caused by the operating pressure.
- The flow probes are therefore suitable for being mounted into existing pipes with diameters of 1/2" to DN 300 upwards.
- The exact positioning of the sensor in the middle of the pipe is granted by means of the engraved depth scale.
- The additional measurement of temperature and absolute The maximum mounting depth corresponds to the respective probe length. (Probe length 220 mm = 220 mm maximum mounting depth). and calculation of the relevant density means that measuring can be carried out for various gases, a wide variety of temperatures and pressures.
Compressed Air Flow Meter Installation Procedure:
:- Compressed Flow meter & Pressure meter installation for Energy Audit purpose to measure the overall compressed air consumption.
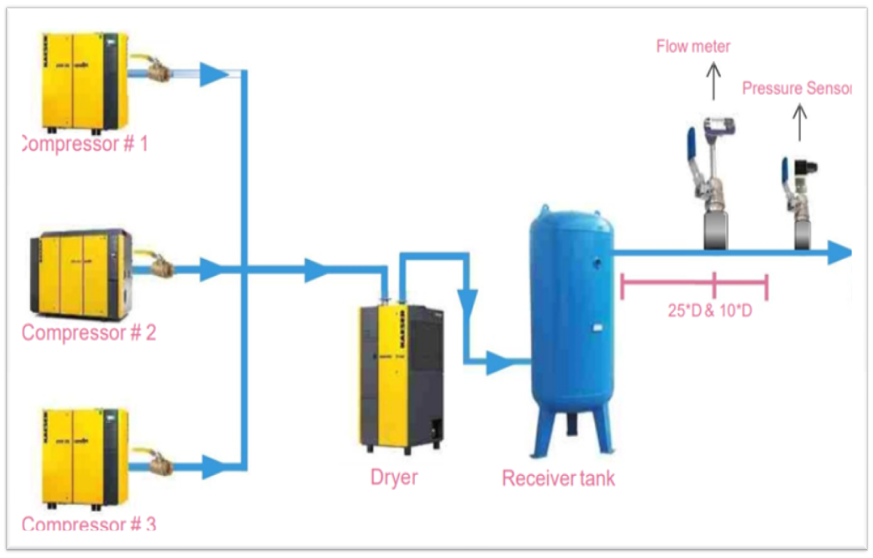